"Put an end to the frequent replacement of capping boards in cell house refineries."
Copper is a highly widely used metal due to its conductivity, corrosion resistance, and versatility. Currently, global demand for copper is at an all-time high, and even the largest producers, such as Chile, Peru, and China, are struggling to keep up with demand, leading to fluctuations in prices. To improve efficiency and reduce the cost of production in copper refineries, it is important to continually explore new innovations and developments. This can help improve the competitiveness of copper producers and enable them to meet the growing global demand for copper.
One factor that can significantly impact the efficiency of the refining process is the maintenance of cellhouse equipment and loss of production due to maintenance tasks. Among the various components in a refinery cellhouse, traditional insulators, also known as capping boards, are often subject to maintenance and replacement due to the excessive wear and tear they experience during the refining process, especially given their traditionally short lifespan. Replacing these insulators can be a labor-intensive and time-consuming process.
If the insulators are not properly maintained or replaced, when necessary, it can lead to problems with the operation of the cells, such as uneven current distribution or difficulty in maintaining proper operating conditions. This can decrease efficiency and reduce production rates. In addition to the impact on efficiency, the need for maintenance and replacement of traditional insulators can also result in lost production due to maintenance and potential shutdowns of the cellhouse.
Traditional vs Permanent Equipotential Insulators
Older technologies of making insulators use low-resistance materials and were made of multiple pieces that were challenging to install and position accurately. This could lead to notable compromises on the rate of production due to the crucial effects of proper electrode alignment in a refinery.
Considering the important role of insulators to have all cells electrically connected and operate at the same potential, a new generation of insulators, known as Permanent Equipotential Insulators, was developed with ultra-high durability and chemical resistance in harsh conditions of a cell house.
High-quality equipotential insulators can have a significant impact on the efficiency of the process in hydrometallurgy or non-ferrous cell houses. This is important because it helps to ensure that the cells are operating at the optimal voltage and current levels, which can improve the overall efficiency of the process. Also, permanent equipotential insulators are more resistant to wear and tear, which can help to extend the life of the cells and reduce the need for maintenance and repairs. These advantages can help to maximize the efficiency and safety of the cell house and to reduce operating costs. Some of the early versions of these insulators have been in operation for over 22 years in copper refineries and over 19 years in zinc refineries while also providing unmatched protection against electrochemical reactions and accelerated corrosion even when subjected to a high concentration of acids up to 100% (Fig. 1). This is a significant improvement compared to the lifetime of traditional insulators which typically ranges from 6 months to 2 years.
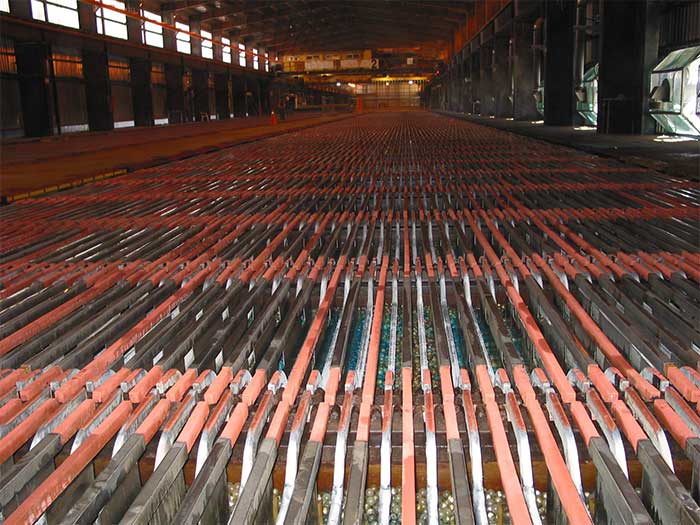
Fig. 1- Permanent Equipotential Insulators made by Pultrusion Technique and installed in a copper refinery near Zaldivar since 1999
The expected lifetime of equipotential insulators
The lifespan of an equipotential insulator in a copper ER – EW facility can vary based on several factors, including the quality and durability of the construction materials, the design and manufacturing process of the insulator, the operating conditions in the electrorefining facility, and the maintenance and care provided to the insulator.
Insulators made from high-quality, corrosion-resistant materials tend to have a longer lifespan. For example, the latest designs use pultruded fiberglass bars made from top-grade, corrosion-resistant raw materials that can withstand the harsh environments found in electro-refineries. Additionally, due to the advanced techniques and processes in manufacturing, they can perform better and are less likely to degrade over time. This is a proven technology, with a unique formulation that resulted from decades of research and development on the selection of compounds in synthetic resins, with top performance such as resistance to temperatures of up to 600 °C and currents of up to 200,000 Amps at 780 Volts.
The operating conditions in the ER & EW facility, such as temperature, humidity, and other environmental factors, can also impact the lifespan of an equipotential insulator. Generally, proper maintenance and care, including regular cleaning, inspections, and prompt repair or replacement of damaged components, can help extend the lifespan of an insulator and reduce the need for replacements (Fig. 2).
The concept of permanent equipotential insulators was developed through the innovation of new design and manufacturing processes that take all these factors into account. As a result, these insulators are less prone to frequent replacements and, as the name suggests, are intended to be permanent.
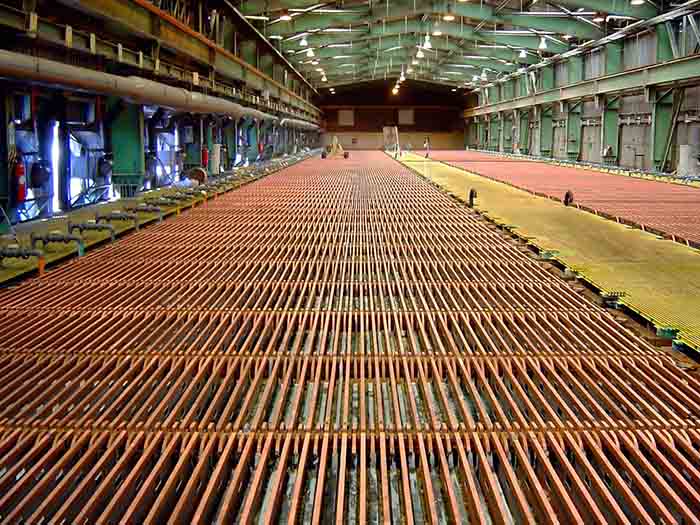
Fig. 2- Permanent Equipotential Insulator in operation since 1994
Advantages of using permanent equipotential insulators
a) Reduction in the Electrical Costs
The alignment and tolerances of electrode seats can significantly affect the overall performance of a refinery. Achieving precise alignment can be challenging with traditional multi-piece insulators. While the design choice may depend on various factors, such as the size and shape of the electrolytic cells, the available space, and the specific requirements of the electrorefining process, insulators made in a single, longer piece with higher precision are more effective at maintaining a consistent electrical distribution throughout the system.
Permanent equipotential insulators are made in a single piece, and often incorporate pultruded fiberglass bars as reinforcement, which are manufactured through a unique process that creates a homogenous, continuous-length structure with a high level of dimensional stability. The precision can go up to 0.4 mm center-to-center, and from the first anode to the last anode at 2.8 mm along an 11-meter length. This helps provide a secure fit and accurate positioning for the electrodes, making the insulators less vulnerable to mechanical stress and other types of damage. This, in turn, can extend the useful life of the insulators and prevent electrical failures and other issues that may result from misaligned electrodes, such as short circuits and uneven electroplating.
b) Better Protection for Electrolytic Cells
Equipotential insulators come in a variety of shapes and designs. Some designs include two side flanges on the sides of the insulator to facilitate a secure fit on top of two adjacent cells. This design, known as the umbrella shape, also includes a special slot for positioning the contact bar and can serve as a protective shield against thermal loads from short circuits and chemical corrosion (Fig. 3). In the event of a short circuit, the insulator can act as a barrier to prevent the flow of electric current from reaching the electrolytic cells, protecting them from the excessive heat and mechanical stress that a short circuit can cause.
When a short circuit occurs, the flow of electric current is redirected from its intended path and directed through an unintended route. This can generate excessive heat and cause the insulator to heat up rapidly, resulting in mechanical stress and other forms of damage. The excessive heat generated by a short circuit can also damage the electrolytic cells under the insulator. These cells are designed to operate within a specific temperature range, and exposure to excessive heat can cause them to become less efficient or fail entirely.
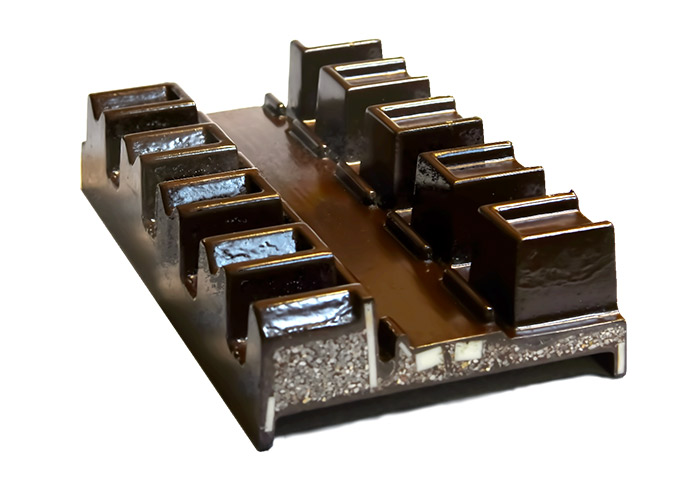
Fig. 3- Umbrella-shaped equipotential insulator
Some equipotential insulators are also designed to protect against chemical corrosion. During the harvest of pure metal from the cathode, the electrolyte splashes as the cathodes are removed from the cell. If the capping board is made of multiple parts, the electrolyte may seep into the joints between them. As the heat of the process causes the water in the electrolyte to evaporate, sulfuric acid becomes more concentrated. At a concentration of over 70%, no plastic material can withstand the corrosive effects of the acid. Studies have shown that even Teflon will break down into black granulated aggregates and powder.
The modern chemical formulation utilized in the production of permanent equipotential insulators with exceptional resistance can endure this harsh environment for more than two decades, and as a result, in the event of an acid spill, the insulator can act as a shield to redirect the acid away from the electrolytic cells and to effectively protect them from damage.
c) Increased Safety
Permanent equipotential insulators provide a continuous and consistent level of insulation, which helps to reduce the risk of electrical accidents and injuries. This is particularly important in hazardous environments, such as copper electro-refineries, where the potential for electrical accidents is very high. For instance, without proper insulation, operators are prone to electrical shocks coming from a potential difference between different parts of the electrical system. The proper function of insulators prevents an electrical current to flow through a person’s body if they come into contact with the system and eliminates the chances of serious injury.
d) Metal refining with higher quality and purity
As mentioned earlier, long-lasting equipotential insulators can improve the efficiency and effectiveness of the electro-refining process. This can help to reduce energy usage and increase productivity, which can ultimately lead to an increase in the production of copper.
Additionally, the use of long-lasting equipotential insulators can also help to improve the quality and purity of the extracted copper. By providing better electrical insulation and reducing the risk of short circuits and other electrical failures, permanent equipotential insulators can help to ensure that the electro-refining process is performed consistently and reliably. This results in copper plating that is of higher quality and purity.
Summary: a wise investment with a high ROI
In summary, on top of all the previously mentioned advantages, permanent equipotential insulators are a good investment for refineries. Even though these insulators are made from premium raw materials and tend to be more expensive than traditional insulators, their longevity and durability can result in a lower frequency of replacements, ultimately leading to cost savings in the long term. These savings, along with the improved efficiency and effectiveness of the electrorefining process due to the insulators’ consistent maintenance of electrical potential, can contribute to a higher return on investment for these insulators. In other words, the initial higher cost of the insulators may be offset by the cost savings from reduced replacements and improved productivity, leading to a more favorable financial outcome and higher return on investment (ROI) in the long run.